News Article
QIMA 2020 Q2 Barometer
COVID-19 Impact: After a Brief Post-Lockdown Rebound, Sourcing from China Plummets 19% in Late March
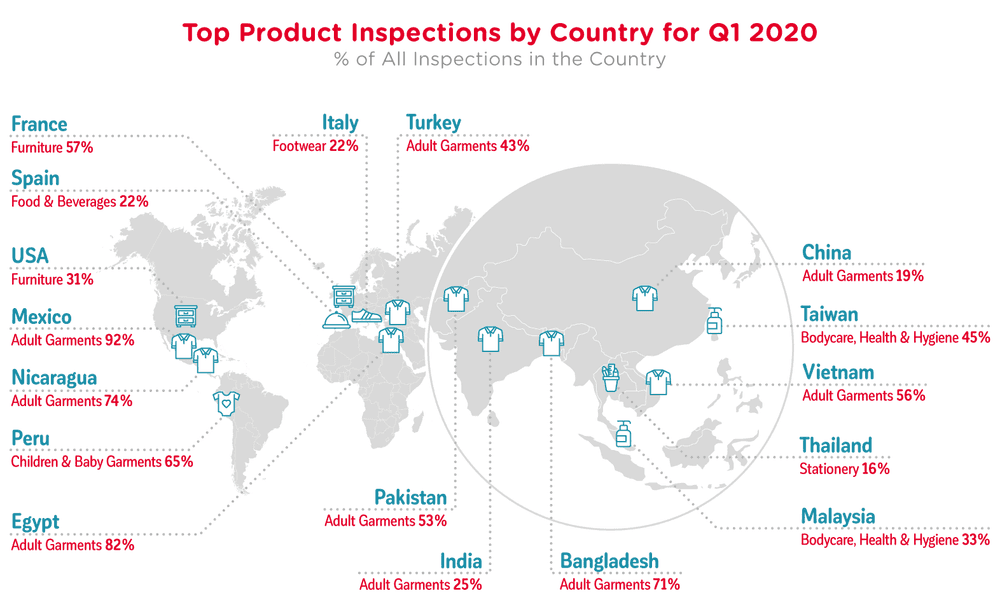
Q1 2020 has been by far the most turbulent quarter since QIMA started analyzing trends in global sourcing, quality and compliance in 2012. Based on data collected from tens of thousands of supply chain inspections and audits performed globally for consumer goods brands and retailers, QIMA's latest quarterly barometer offers a unique opportunity to witness the unfolding impact of the COVID-19 pandemic on global sourcing.
China's Manufacturing Goes from Coronavirus Lockdown to Demand Shock
In the first two months of 2020, the China shutdowns due to the COVID-19 outbreak in Hubei province had exacerbated the traditional first-quarter slowdown of Chinese manufacturing. Meanwhile, QIMA data showed that demand for inspections and audits in the three weeks of February following the Lunar New Year celebrations plummeted by -75% YoY.
In March, as lockdowns began to lift in China, local manufacturing rallied, and by the week of March 16, inspection and audit volumes were poised to catch up with 2019 levels. However, this rebound was cut short as buying countries in the West, in turn, began imposing quarantine measures, and the week of March 23 saw inspection and audits volumes in China collapse again, down -19% YoY vs. 2019.
In a Preview of Post-COVID Buying Patterns, Brands Had Started Shifting Sourcing to Still-Open Regions
In a late February QIMA poll of 200+ businesses with global supply chains, 87% of respondents pointed out that the coronavirus pandemic will trigger significant changes in how they manage their supply chain going forward. To mitigate factories shutdowns, more than half of respondents affected by the pandemic noted that they had begun switching to suppliers in unaffected regions.
For instance, in January-February 2020, demand for inspections and audits from North American buyers surged +45% YoY in Southeast Asia (with Vietnam, Myanmar and the Philippines in the lead), and +52% in South Asia, where Bangladesh remained a go-to destination for Textile and Apparel brands (+48% YoY increase in global demand for Textile and Apparel inspections in the first two months of 2020).
However, as more lockdowns began taking effect in March, both in the West and in manufacturing hubs, demand began to plummet across the board. In the last week of March alone, demand for inspections from North American and European brands and retailers dropped by -26% YoY and -16% YoY, respectively – providing the first taste of the impact to come as global brands shut stores worldwide and the entire consumer goods supply chain is bracing for lengthy turmoil.
This is particularly obvious in manufacturing countries and regions that had initially reaped the benefits of the shutdowns in China: in Vietnam, demand for inspections and audits, after surging 61% YoY in the first two months of 2020, plummeted -12% YoY during the last week of March.
Bangladesh, where garment factories had remained open despite the quarantine, was a temporary exception to this rule with inspection demand spiking +76% YoY in March – but with the news of a full lockdown breaking on April 6th, it now looks that the country is likely to see a decline in demand.
Related Disruptions: Is COVID-19 a One-Two Punch for Supply Chain Sustainability?
As a side effect of COVID-19, 2020 will likely prove a particularly challenging year for sustainability in supply chains, as the ebb and flow of lockdowns globally exacerbates the ethical risks inherent in emerging sourcing regions.
With shutdowns and quarantines setting in across buying and manufacturing regions alike, most factories are shifting into "survival mode", with ethics and sustainability concerns falling to the very bottom of their agenda. Worker safety in particular is a pain point: during audits of factories still open during Q1, QIMA auditors found Health & Safety among the most pressing issues, with critical H&S violations recorded in 5.5% of factories. In addition, almost half of factories surveyed by QIMA structural auditors and civil engineers were found in need of improvement for fire safety, including 4.5% that had critical violations.
As Non-Essential Consumer Goods Come to a Halt, Supply Chains Pivot to Accommodate Surging Demand for PPE
Meanwhile, as the number of infections grows, so does the global shortage of personal protective equipment (PPE), and the shift of global supply chains from non-essential goods to PPE is creating new quality control challenges.
To help address PPE shortages and give back to the global communities they serve, brands like Zara, Gap, Hanes and LMVH have pivoted their manufacturing to personal protective equipment, and purchase orders sent to Chinese manufacturers have been booming to meet the global demand. However, managing such a surge in manufacturing is proving challenging for both buyers and manufacturers, as speed of delivery cannot come at the expense of quality and conformity for such vital equipment: something that has been recently emphasized by China's government recent announcement of stricter controls over PPE factories.
Accordingly, QIMA has seen demand for quality control services of PPE increase +80% between January and March, with inspection scopes covering everything from workmanship quality to ensuring that factories have the required certificates and export licenses.
What Will Be the New Normal of Global Sourcing?
The unprecedented levels of global trade disruption and uncertainty triggered by COVID-19 make reliable forecasting all but impossible. Nevertheless, the observations and trends recorded by QIMA point to several probable outcomes of this still-unfolding global crisis.
With the current crisis further underscoring the risk of supply chains keeping all eggs in one basket, geographical diversification of sourcing will soar to new heights when global trade resumes. In particular, the near-shoring trend of 2019 can be expected to continue and accelerate; while the future of Asian manufacturing regions outside China will hinge on their survival of the COVID-19 age.
Brands and retailers that weather the storm are likely to end up with greatly overhauled supplier portfolios, made up by factories that manage to survive the lockdowns. During that time, supplier audits will be instrumental for ensuring quality and compliance: as such manufacturers will be tempted to operate in the stripped-down mode that had enabled their survival. Furthermore, the 2020 pandemic will likely push brands and manufacturers to revisit existing supplier auditing frameworks and put sanitation and hygiene checks at the top of checklists.
Finally, the dawning recession will likely act as a catalyst for brands to transform their supply chain into leaner, more agile operations. To keep their sourcing operations on par, brands will need to accelerate the digitization of their supply chain management and invest in solutions that help achieve supply chain visibility, map risks and identify quality and compliance issues in real time.
QIMA Barometer Key KPIs
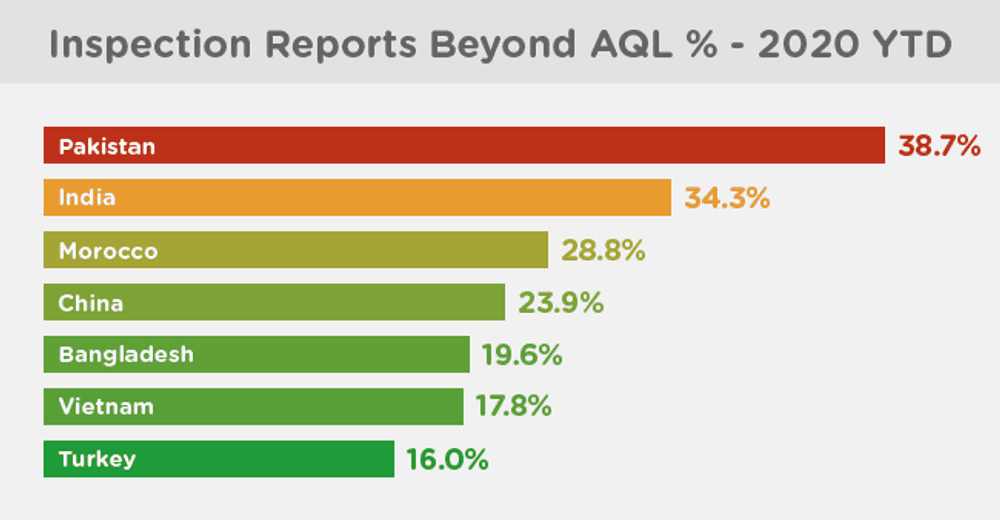
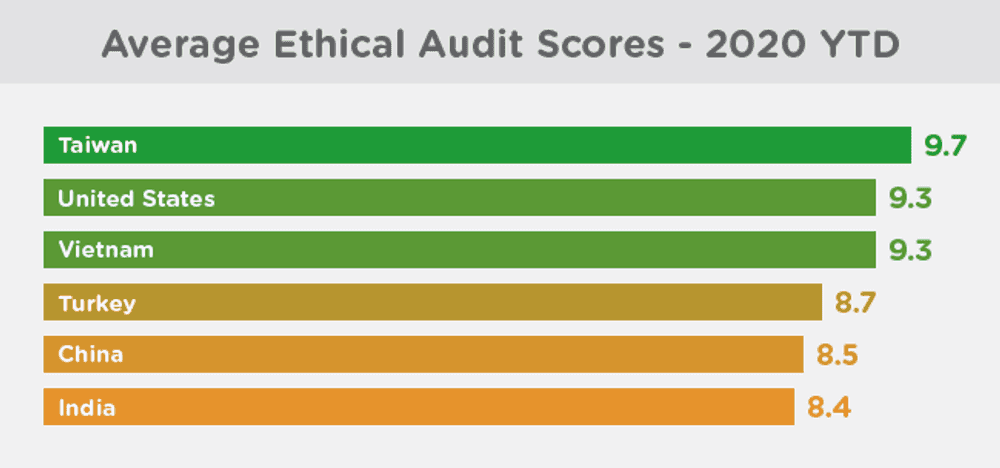
Press Contact
Email: press@qima.com