What is a Technical Audit
When it comes to partnering with a new supplier or enhancing the performance of an existing one, ensuring their adherence to your standards is crucial. That's where auditing comes in. By conducting a thorough review of their performance against pre-established quality criteria, you can make informed decisions and identify areas for improvement.
A QIMA technical audit provides a comprehensive assessment of a factory’s systems and processes and identifies ways to maintain or improve quality levels, giving you the confidence that your standards will be met or any shortcomings will be addressed effectively.
Our Solutions
When we carry out a technical audit, we make an independent, robust and comprehensive assessment of your supplier’s (or potential supplier’s) capabilities.
The exact checks that are carried out in a QIMA audit can be tailored to your particular industry or product following our guidance. Alternatively, they can be tailored to your own in-house quality requirements.
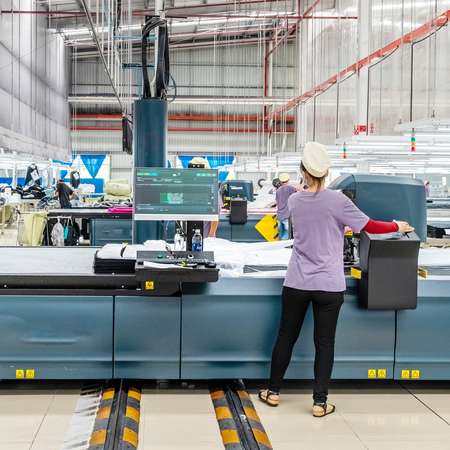
Our Audit Protocol Covers
Quality management systems – how a facility plans, manages and documents quality control.
Resources management – how a facility manages quality-related resources, such as personnel or quality control equipment.
Stock management – how materials and in-process and finished products are stored and handled.
Incoming material inspection - how quality issues in incoming materials are addressed.
Production processes – workshop management and quality control during production
Quality control processes before shipment and packing procedures – packing line organization and shipment preparation as well as quality control procedures before shipment
Measurement, analysis and improvement of quality levels – factory internal audits and management of quality data
Any other specific instructions from the client
Why Perform a Technical Audit?
Verify that a new supplier is capable of meeting your requirements.
Manage quality risks and prevent quality failings by ensuring adequate in-factory systems are in place.
Identify ways to improve quality standards.
Ensure that quality and safety standards are maintained across multiple suppliers.
Need more information?
By contacting QIMA you agree to our privacy policy and terms and conditions.
What You will Receive Following An Audit:
After an audit is complete, the findings are delivered to you in a comprehensive report. This will be available within 48 hours. Where issues are identified, a corrective action plan (CAP) is also provided to your supplier. This will outline any actions they need to take to bring quality standards up to the right level. Our specialist auditors also provide an overall score that represents the level of risk in your supplier.
Progress on corrective actions can be measured through a follow-up audit, desktop review and/or phone calls. You can also manage the implementation of the corrective action plan through our factory improvement services.
Technical audits are carried out by a senior QIMA auditor or an auditor leader with at least 5 years of experience in the field.
The QIMA Benefits
In-depth local knowledge with auditors attuned to the culture, laws and practices of their region.
CSR experts receive regular training on regulations and best practice.
Global coverage across 100 countries in Asia, Africa, Europe, North and South America.
Continuous improvement approach drives long-term change and empowers suppliers to act.
Online program management book audits, make payments and download detailed reports.
Custom compliance dashboard to assess supplier performance, track progress and visualize your supply network.